- If a customer cannot be supplied immediately, customer dissatisfaction may arise
FINANCE
The importance of inventory control
Inventories or goods in stock refer to the amount of fixed assets or goods that a company has at a specific moment in time. Inventory control is generally an issue that is poorly addressed by SMEs.
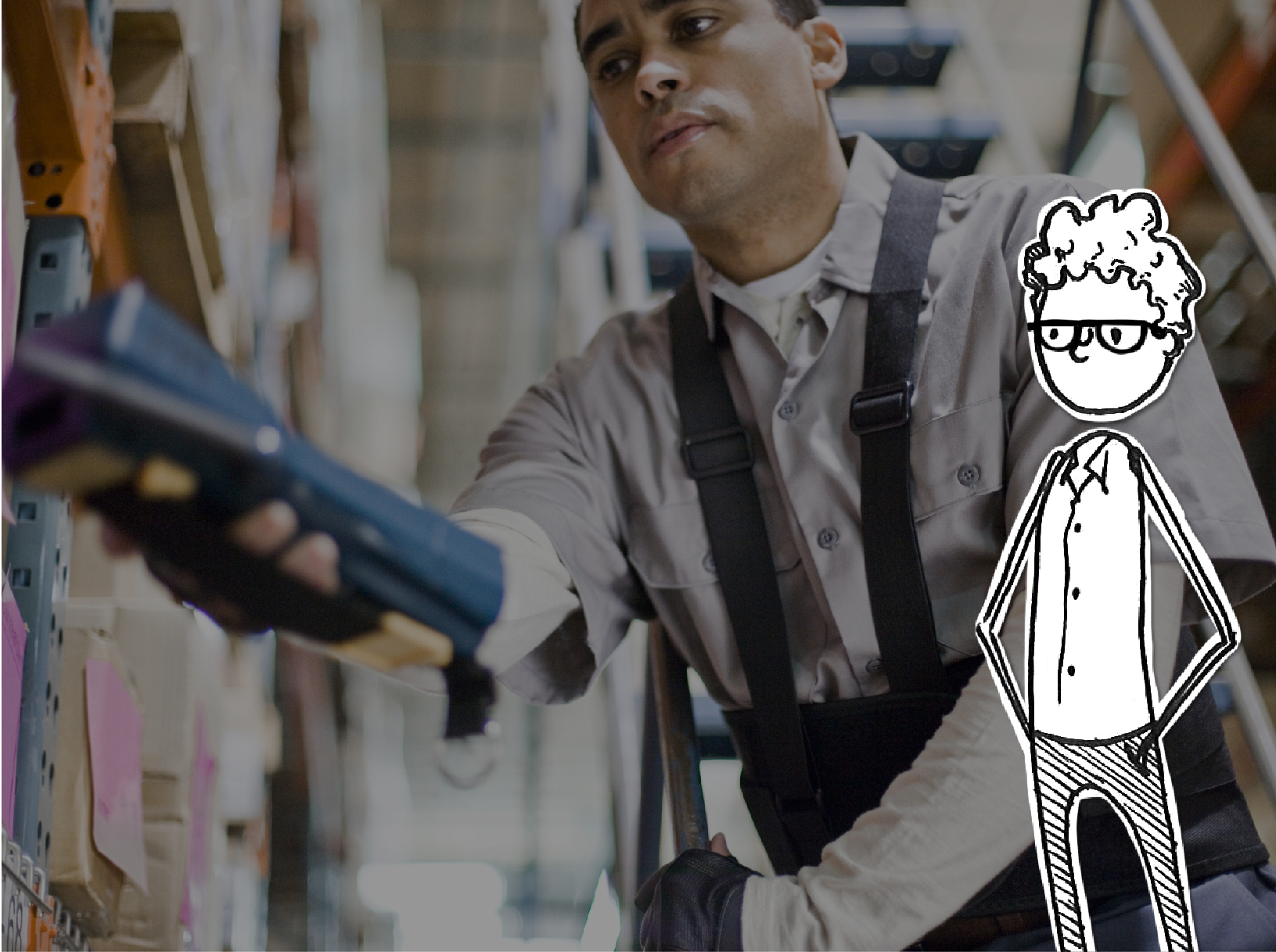
HIGHLIGHTS
Obtaining profit largely depends on generating sales since they are the driving force of any company. However, if inventory management is not effectively handled there is a chance of not being able to meet the product’s demand. This situation can result in customer dissatisfaction, who eventually might choose a competitor, which in turn will generate profit losses for the company.
The Inter-American Investment Corporation (IIC) describes the importance of keeping a detailed record of procedures for ordering and receiving a consignment of goods toensure that enough inventory is being held, that there is no duplication of orders and that quality is maintained.
There should be controls over the following functions:
-The ordering of inventories
-The purchase of inventories
-The receipt of goods into store
-Storage
The IIC recommends small and medium companies (SMEs) to at least evaluate product entry and exit operations using some basic control techniques. There are several reasons to effectively manage inventory since holding costs may be expensive. It is important for a company to identify the ideal amount of products to keep in stock so that it does not generate excessive costs in this regard.
Furthermore, failing to keep adequate levels of raw material will have a negative impact on profit due to the inability of producing the good that is being sold. Likewise, if inventory with a short shelf life is not used or sold, its value may decline or become worthless. Additionally, if a customer cannot be supplied immediately, customer dissatisfaction may arise.
Inventory control levels
Based on an analysis of past inventory usage and delivery times, a series of control levels can be computed and used to maintain inventories at their optimum level. These levels will determine when to order and how much to order to satisfy demand.
- Reorder level:When inventories reach this level, an order should be placed to replenish inventories. The reorder level is determined by considering the following:
-The maximum rate of consumption (demand generated per day)
-The maximum lead time (delivery time of a new order)
The maximum lead time is the time between placing an order with a supplier, and the inventory becoming available for use. The basic formula for determining the reorder level is as follows:
Reorder level = maximum usage per day × maximum lead time(days)
Example: ABC is a shoe company. It sells approximately 500 units per day. Its supplier takes one week to deliver the order. Therefore, the inventory manager must make the order before the stock falls below 3,500 units (500 usage units per day multiplied by 7 days of waiting time) to avoid shortage.
- Minimum inventory level: This is a warning level to draw management attention to the fact that inventory is approaching a dangerously low level. The inventory level should never drop below this point since it may imply a possible interruption of operations. It is determined by computing the estimated time between the start of production to the point in which the product reaches the end consumer. The basic formula for determining the minimum level is as follows:
Minimum level = reorder level – (average usage per day × average delivery time to customer)
Example: ABC has reorder level of 3,500 units (example above). It has an average daily demand of 500 units and it takes five days to deliver the final product to the client. The inventory manager must keep a minimum level of 1,000 units (3,500 reorder units – 500 units demanded daily x 5 days of delivery to the client). It is essential to keep this indicator in mind to avoid the risk of not having sufficient levels to cater for the demand.
KEYWORDS
Follow Us